„One for all“ - Change of software at Siemens
The Siemens group is currently introducing the leading software comm.fleet and comm.cars from community4you for the fleet management and vehicle procurement in Germany. Other countries will follow.
Norbert Wiedmann can look back on an eventful history of fleet management at Siemens. As the current Director of Global Commodity Fleet started his service almost 30 years ago as a fleet manager, he counted several thousand vehicles in service and management. The former part of the fleet dominated at that time. From a current perspective a manageable size and responsibility for him over the years, the fleet tended to increase due to acquisitions and growth, especially in the user-chooser area. At peak times, over ten years ago, as Siemens Nixdorf was still part of the Siemens group, the German fleet totaled around 20,000 units. Currently the fleet has plateaued at around 13,500 vehicles, about 8,500 of which are driven by the sales representatives, 3,000 by the service technicians and 2,000 by the management. But the volume can quickly increase again, for example if a new company should join the group. Thus not only the number of cars, but also the constant change over time requires a high degree of transparency and flexibility in the fleet management.
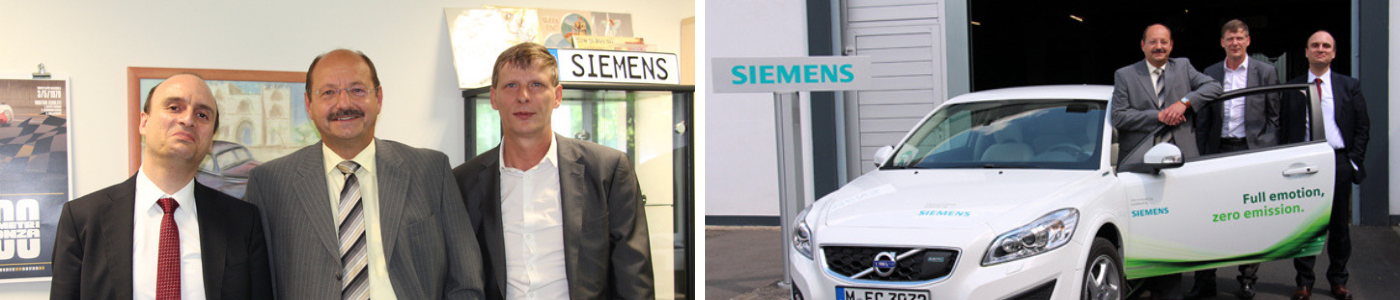
Photos: Autoflotte
Maximal automation | A major concern in the area of Global Commodity Fleet is therefore the constant automation of as many processes as possible, while at the same time keeping them internal. "We are permanently working on process automation within fleet management, while at the same time striving to keep our employees as the link to the user" says Wiedmann. […] The aim is therefore to balance the diverse tasks in these areas of tension. Both flexibility and autarky as well as transparency and data integrity play a central role.
Data management | In the fleet of Siemens the focus lies therefore on the intelligent management of data. Where does it come from? What level of detail should it have? Where should it be stored? And how can it be accessed in-house, without having to enter it laboriously by hand?
"These are questions we must ask ourselves constantly in order to manage the information and processes since the tasks are extremely complex," argues Wiedmann. [...] "At the moment of approval and receipt of a company car, a whole series of processes starts such as the calculation of cash benefits, which must be retriggered and work across departments."
In order to map these complex processes the previous software often did not suffice. "That is why we regularly had to develop our own modules", says the fleet manager. As a result, he started to search for a new solution.In the phase of implementation | With community4you Siemens has found a solution for the fleet management thanks to their software comm.fleet as well as with comm.cars as a procurement tool for vehicle-eligible employees and executives. After the successful rollout of comm.fleet in Austria, which has been the first country to migrate to the new software, the Siemens group is now in the process of implementing comm.fleet in Germany as well. In September last year the company issued the order. The start of the rollout by the service provider was in February. Until October 1st the software should be adapted and implemented according to the specific requirements of Siemens. Subsequently the introduction of comm.cars will follow. The web-based procurement platform shall be available to all users from the beginning of 2015. Both systems will operate on the basis of a common database and provide access to information to users according to their needs and rights.
Wiedmann explains what this means for the utilisation of comm.cars: "When the user logs in with his company ID, the system has at disposition all the parameters, such as name, driver category within the car policy and the expiration date of the leasing contract. comm.cars can show the driver his possibilities and authorisation limits, and initiate the corresponding processes for an order."
With the implementation in Austria and Germany the work is not over though.
"Other countries, mainly in Eastern Europe, are waiting in the queue. In the future we will continue to offer the software as a solution in all regions where a legacy system must be replaced or no system was used until then. This concerns for example countries working together with several leasing companies," says Wiedmann. Advantages for Siemens | With the implementation Siemens aims at raising the level of automation. The company from Chemnitz has won the bid for a number of reasons. Wiedmann explains this in particular with the flexibility of the system and its reliability that result from the development of the system on the basis of an integration platform owned by community4you - open-EIS.
As a matter of fact, we are one of worldwide only six companies – along with IBM, Microsoft, Oracle, SAP and Software AG - that can afford this at 100 percent, adds Uwe Bauch, President of community4you AG. “Furthermore this gives us the freedom to provide interfaces to all programs, because due to our own platform we are not limited in the communication with other programs, languages and protocols and we can adapt to any IT-infrastructure.”
This mixture allows a free fleet management, which involves the integration of all data sources and a customer-specific mapping of processes.
"That implies a completely new level of automation," says Wiedmann. "This is also true for all other countries, which will receive a country-specific customised solution in their language.” Wiedmann says further: "At the same time Siemens can rely on data integrity and reliability despite the integration of all possible data sources in the system".
Siemens has always had this requirement as a benchmark, but so far no service provider could meet it. For this reason as well, in the past extensions were mostly implemented through in-house developments if the software did not provide this capability.
Wiedmann sums up: "When in our search for a software and while dealing with the question `Make or buy?’ we found an external solution at community4you which complies with our needs from a professional, automation technical and a data privacy perspective, the decision was easy."
Process Mapping | The fleet management team placed a particular emphasis on the professional competence and the continuous adaptation to legal requirements such as vehicle tax and cash benefits as well as the integration of company specific parameters.
"Thus we can integrate the complex processes without having to make great investments of time and money in in-house developments," says Wiedmann.
An example for him is the management of fuel cards: Each employee receives one. But not everyone is allowed to use it for the same purposes. While one employee can only fill up fuel, another one is allowed to wash his car as well. Yet another one may also be allowed to make use of additional services with it. Depending on this a process is needed that takes this into account and implements it, and at the same time when an order is submitted ensures that the fuel cards arrive directly at the homes of the employees from Garmisch up to the North Sea.
"In the future this will be done automatically, whereby we retain the data sovereignty and the logistical capability to control this accordingly," said Wiedmann.
Modeled Software | In general with comm.fleet the customisation process is faster.
Lavinio Cerquetti, as Vice President of community4you AG in charge of business operations, explains why and how this is possible: ”The software is no longer developed by programmers, but modeled by software architects. This means that the software is completely based on a model driven, multi-tier architecture. We have developed our know-how in models, for example the procurement of vehicles or the management of claims and out of this we have generated in a semi-automated manner a great part of the processes.”
In practice, as a result of this approach complex adaptation processes are eliminated, in which the 100th code location must be found and changed. Rather, the graphic representation of the models is changed and out of them the adapted software artifacts are generated.
Cerquetti: "This whole process is much faster, less error-prone and interlocked so that the customer achieves much sooner the return on investment."
The fleet manager himself | Here Mr. Wiedmann expects a quantum leap forward with the new systems. Especially as comm.fleet puts the team in the position to perform itself the so-called customising of the software.
"This is an essential feature: the possibility to customise the system according to the needs of the customer without much effort and without the staff of the service provider," says Wiedmann. Cerquetti explains the background: "Due to the fact that the program is based on an abstract model and all tools that are necessary for the customising are included within the program, each customer is able to perform itself the customising after a training in system administration."
Thus he can create or change by itself all masks, dialogs, data views, menus, and reports including the parameters for a user, a user group, a client or a country.
"In general the program is always conform to the legal statutory conditions of the country," says Bauch. "Furthermore the number of vehicles is not relevant for the software, so that it can expand with the customer."
The system architecture provides a central cross-border database that is specifically mapped and available in different countries.
The training of the Siemens employees of the Global Commodity Fleet team will take place shortly. Ten to fifteen employees shall work afterwards with comm.fleet, whilst the number of comm.cars users will definitely exceed 10,000 once the software is implemented.
Source: Autoflotte 08/2014
Photos: community4you AG
Data management | In the fleet of Siemens the focus lies therefore on the intelligent management of data. Where does it come from? What level of detail should it have? Where should it be stored? And how can it be accessed in-house, without having to enter it laboriously by hand?
"These are questions we must ask ourselves constantly in order to manage the information and processes since the tasks are extremely complex," argues Wiedmann. [...] "At the moment of approval and receipt of a company car, a whole series of processes starts such as the calculation of cash benefits, which must be retriggered and work across departments."
In order to map these complex processes the previous software often did not suffice. "That is why we regularly had to develop our own modules", says the fleet manager. As a result, he started to search for a new solution.In the phase of implementation | With community4you Siemens has found a solution for the fleet management thanks to their software comm.fleet as well as with comm.cars as a procurement tool for vehicle-eligible employees and executives. After the successful rollout of comm.fleet in Austria, which has been the first country to migrate to the new software, the Siemens group is now in the process of implementing comm.fleet in Germany as well. In September last year the company issued the order. The start of the rollout by the service provider was in February. Until October 1st the software should be adapted and implemented according to the specific requirements of Siemens. Subsequently the introduction of comm.cars will follow. The web-based procurement platform shall be available to all users from the beginning of 2015. Both systems will operate on the basis of a common database and provide access to information to users according to their needs and rights.
Wiedmann explains what this means for the utilisation of comm.cars: "When the user logs in with his company ID, the system has at disposition all the parameters, such as name, driver category within the car policy and the expiration date of the leasing contract. comm.cars can show the driver his possibilities and authorisation limits, and initiate the corresponding processes for an order."
With the implementation in Austria and Germany the work is not over though.
"Other countries, mainly in Eastern Europe, are waiting in the queue. In the future we will continue to offer the software as a solution in all regions where a legacy system must be replaced or no system was used until then. This concerns for example countries working together with several leasing companies," says Wiedmann. Advantages for Siemens | With the implementation Siemens aims at raising the level of automation. The company from Chemnitz has won the bid for a number of reasons. Wiedmann explains this in particular with the flexibility of the system and its reliability that result from the development of the system on the basis of an integration platform owned by community4you - open-EIS.
As a matter of fact, we are one of worldwide only six companies – along with IBM, Microsoft, Oracle, SAP and Software AG - that can afford this at 100 percent, adds Uwe Bauch, President of community4you AG. “Furthermore this gives us the freedom to provide interfaces to all programs, because due to our own platform we are not limited in the communication with other programs, languages and protocols and we can adapt to any IT-infrastructure.”
This mixture allows a free fleet management, which involves the integration of all data sources and a customer-specific mapping of processes.
"That implies a completely new level of automation," says Wiedmann. "This is also true for all other countries, which will receive a country-specific customised solution in their language.” Wiedmann says further: "At the same time Siemens can rely on data integrity and reliability despite the integration of all possible data sources in the system".
Siemens has always had this requirement as a benchmark, but so far no service provider could meet it. For this reason as well, in the past extensions were mostly implemented through in-house developments if the software did not provide this capability.
Wiedmann sums up: "When in our search for a software and while dealing with the question `Make or buy?’ we found an external solution at community4you which complies with our needs from a professional, automation technical and a data privacy perspective, the decision was easy."
Process Mapping | The fleet management team placed a particular emphasis on the professional competence and the continuous adaptation to legal requirements such as vehicle tax and cash benefits as well as the integration of company specific parameters.
"Thus we can integrate the complex processes without having to make great investments of time and money in in-house developments," says Wiedmann.
An example for him is the management of fuel cards: Each employee receives one. But not everyone is allowed to use it for the same purposes. While one employee can only fill up fuel, another one is allowed to wash his car as well. Yet another one may also be allowed to make use of additional services with it. Depending on this a process is needed that takes this into account and implements it, and at the same time when an order is submitted ensures that the fuel cards arrive directly at the homes of the employees from Garmisch up to the North Sea.
"In the future this will be done automatically, whereby we retain the data sovereignty and the logistical capability to control this accordingly," said Wiedmann.
Modeled Software | In general with comm.fleet the customisation process is faster.
Lavinio Cerquetti, as Vice President of community4you AG in charge of business operations, explains why and how this is possible: ”The software is no longer developed by programmers, but modeled by software architects. This means that the software is completely based on a model driven, multi-tier architecture. We have developed our know-how in models, for example the procurement of vehicles or the management of claims and out of this we have generated in a semi-automated manner a great part of the processes.”
In practice, as a result of this approach complex adaptation processes are eliminated, in which the 100th code location must be found and changed. Rather, the graphic representation of the models is changed and out of them the adapted software artifacts are generated.
Cerquetti: "This whole process is much faster, less error-prone and interlocked so that the customer achieves much sooner the return on investment."
The fleet manager himself | Here Mr. Wiedmann expects a quantum leap forward with the new systems. Especially as comm.fleet puts the team in the position to perform itself the so-called customising of the software.
"This is an essential feature: the possibility to customise the system according to the needs of the customer without much effort and without the staff of the service provider," says Wiedmann. Cerquetti explains the background: "Due to the fact that the program is based on an abstract model and all tools that are necessary for the customising are included within the program, each customer is able to perform itself the customising after a training in system administration."
Thus he can create or change by itself all masks, dialogs, data views, menus, and reports including the parameters for a user, a user group, a client or a country.
"In general the program is always conform to the legal statutory conditions of the country," says Bauch. "Furthermore the number of vehicles is not relevant for the software, so that it can expand with the customer."
The system architecture provides a central cross-border database that is specifically mapped and available in different countries.
The training of the Siemens employees of the Global Commodity Fleet team will take place shortly. Ten to fifteen employees shall work afterwards with comm.fleet, whilst the number of comm.cars users will definitely exceed 10,000 once the software is implemented.
Source: Autoflotte 08/2014
Photos: community4you AG
08/06/2014